How to Do Daily Maintenance of Inclined Belt and Flat Belt in Belt Concrete Mixing Plant
In belt concrete mixing stations, flat belts and inclined belts (hereinafter collectively referred to as belts) are used to transport aggregates during work, which greatly improves the efficiency of the entire mixing station's automated production process. Once a problem occurs, the entire production task must be interrupted. Therefore, it is very important to master some common belt fault handling methods and daily belt maintenance. Let's talk about this topic together today.
In general, the concrete batching plant belts are divided into flat belts and inclined belts. The flat belt is under the batching bin and is responsible for transporting raw materials such as aggregates to the inclined belt, while the inclined belt is responsible for transporting raw materials to the middle bin of the mixing host. The working methods of the two are also the same, so let's explain the common faults of the inclined belt in detail below.
I. Common Faults
1. Belt Deviation
Belt deviation is the most common fault phenomenon. The reason for its occurrence is that the belt is subjected to unbalanced force in the width direction, and the belt will deviate in the direction of greater tension.
Belt deviation will cause aggregate leakage during transportation, increase belt working noise, and if the deviation is serious, it will cause serious wear on one side of the belt. Therefore, it is necessary to pay close attention to the working condition of the belt in daily production.
Actual causes and treatment methods:
a. The belt roller is stained with dirt and other debris, which causes the diameter of the roller to increase, resulting in uneven force on the belt. This phenomenon is relatively common. It is mostly because the aggregate contains a lot of mud and sand, which is slowly stuck to the roller during movement. This requires regular removal of debris from the roller. At the same time, installing a scraper on the belt is also a very effective method.
b. The belt expands and contracts with heat, causing its length to change. The vibration amplitude during the working process increases, which will also cause the belt to deviate. Generally, more load-bearing blocks need to be added to the tensioning mechanism to make the belt subject to greater tension in the direction of movement.
Belt deviation treatment method:
a. Adjust the roller bracket
Which direction the belt deviates, the roller bracket on the corresponding side should be adjusted according to the running direction of the belt, or the roller bracket on the other side should be adjusted in the opposite direction. Generally, it is fine-tuned. Do not change the displacement distance of the roller drastically. After the adjustment is completed, it must be tested for a period of running time to ensure that it does not deviate, which can be considered as a real adjustment.
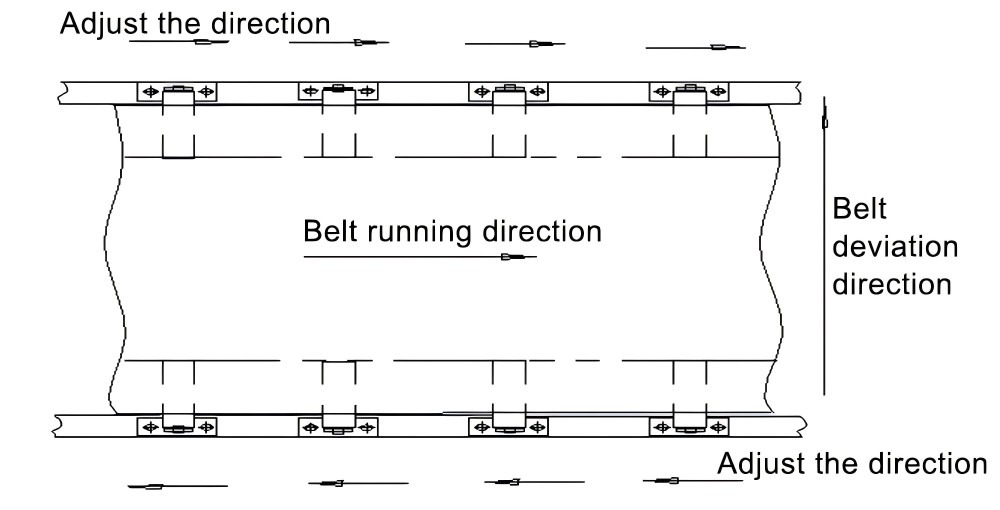
b. Adjust the redirection roller
Generally, the roller at the end of the belt is adjusted, which is achieved by the displacement of the roller mounting seat. In which direction the belt deviates, the mounting seat of the redirection roller on the corresponding side needs to be tightened to tighten the belt, or the mounting seat on the other side needs to be loosened. At the same time, this process also needs to be fine-tuned slowly, and it must not be adjusted too much at one time.
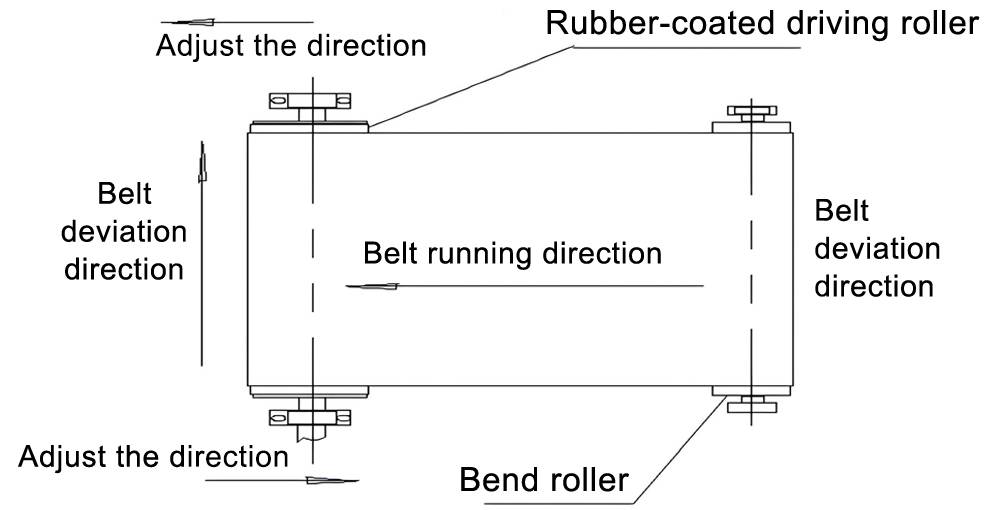
2. Belt Cracking Treatment
Cracking includes transverse cracking and longitudinal cracking. Transverse cracking refers to cracking in the direction perpendicular to the direction of belt movement. It usually occurs mainly at the bonding point of the belt. The belt needs to be cut off and then re-bonded, or repaired. The treatment of longitudinal cracking is more troublesome. It may be that the belt scrapes against a sharp object during operation, causing it to be severely worn and cracked. Generally, longitudinal cracking requires the replacement of the entire belt.
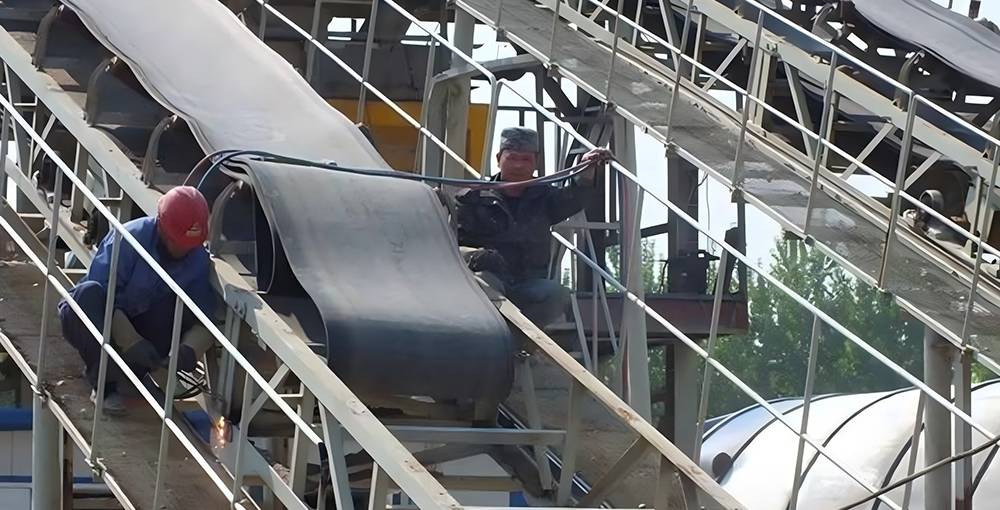
2. Daily Maintenance of Belts
1. Check regularly and remove foreign matter on the rollers.
2. If there are damaged rollers, please replace them immediately
3. For the bearing seat of the belt redirection roller, lithium-based grease needs to be added regularly to ensure the lubricity of the bearing.
4. The belt fender needs to be installed and tightened according to needs. It needs to be tighter in the summer rainy season, and the scraper can be made of some rubber material.
5. If you don't work in winter, you can remove all the counterweights of the belt to ensure good elastic deformation of the belt.
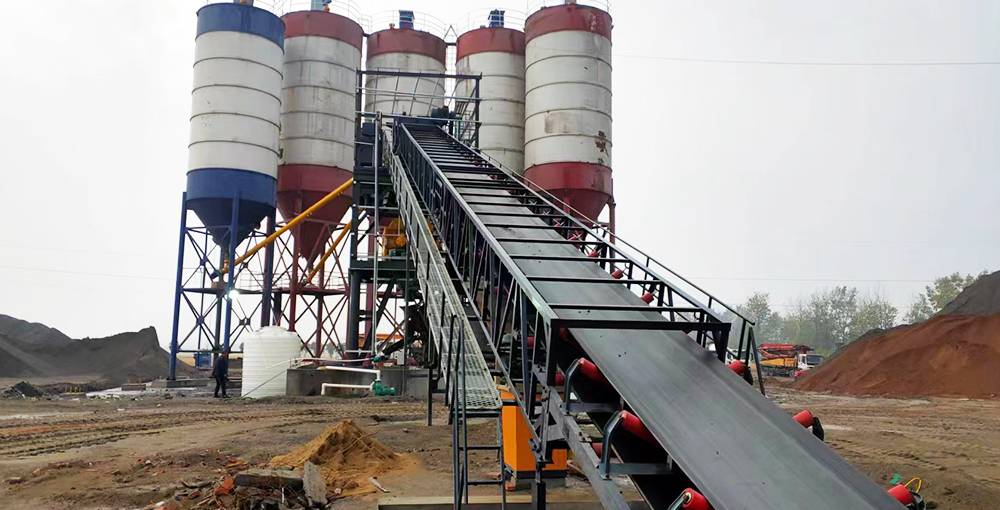
Through the above description, I believe you have your own experience in the maintenance and maintenance of the mixing station belt. If you want to extend the service life of the belt, please do the above work accordingly.