Do You Know the Common Problems and Solutions of Concrete Mixing Plant?
The application of prevention and control of common quality defects in concrete has become an essential link in concrete construction. In the mixing process of concrete in the mixing station, there are often some problems, which bring trouble to the construction progress and quality. This paper analyzes the causes of common problems in mixing concrete and gives a series of solutions.
I. Pumping Concrete Slump Loss, Slump Instability Problem
Cause
1. Poor adaptability of concrete admixture and cement causes rapid slump loss of concrete.
2. The content of concrete admixture is not enough, and the effect of retarding and plastic preservation is not ideal.
3. The weather is hot, and some additives fail at high temperature; Water evaporates quickly; Bubble overflow causes rapid slump loss of fresh concrete.
4. The initial slump of concrete is too small, and the unit water consumption is too small.
5. The poor coordination between the construction site and the mixing station makes the tank car press and jam for too long, resulting in excessive slump loss of concrete.
6. Concrete mixing weighing system measurement error is big, unstable.
7. Coarse and fine aggregate moisture content changes.
8. Cement mixed warehouse storage, mixed use.
Solutions
1. Adjust the concrete admixture formula, make it adapt to the cement. Before construction, be sure to do the adaptability test of concrete admixture and cement.
2. Adjust the concrete mixture ratio, increase or decrease the sand ratio and water consumption, and adjust the initial slump of concrete to more than 200 mm.
3. Adding proper amount of fly ash to replace part of cement.
4. Appropriately increase the dosage of concrete admixture, and adjust the retarding ingredients in the admixture (especially when the temperature is much higher than usual).
5. To prevent moisture evaporation too fast, bubble overflow too fast.
6. Choose slag cement or pozzolanic cement.
7. Improve the water-retaining and cooling devices of concrete transport vehicles.
8. The accuracy of measuring equipment shall meet the relevant regulations, and it shall have a valid certificate issued by the legal measurement department, and strengthen self-inspection to ensure accurate measurement.
9. Strengthen the detection of aggregate moisture content, change, timely adjust the mixture ratio.
10. The incoming cement shall be stored and used respectively according to the manufacturer, variety and label.
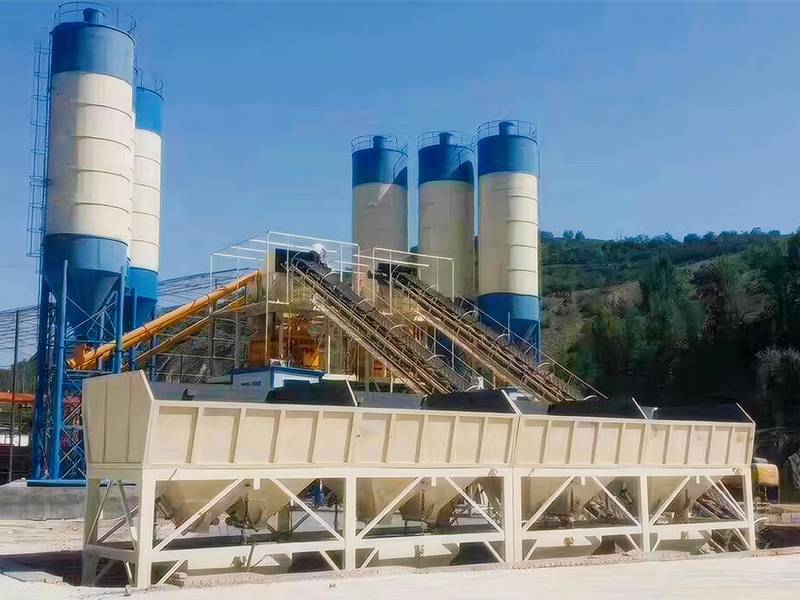
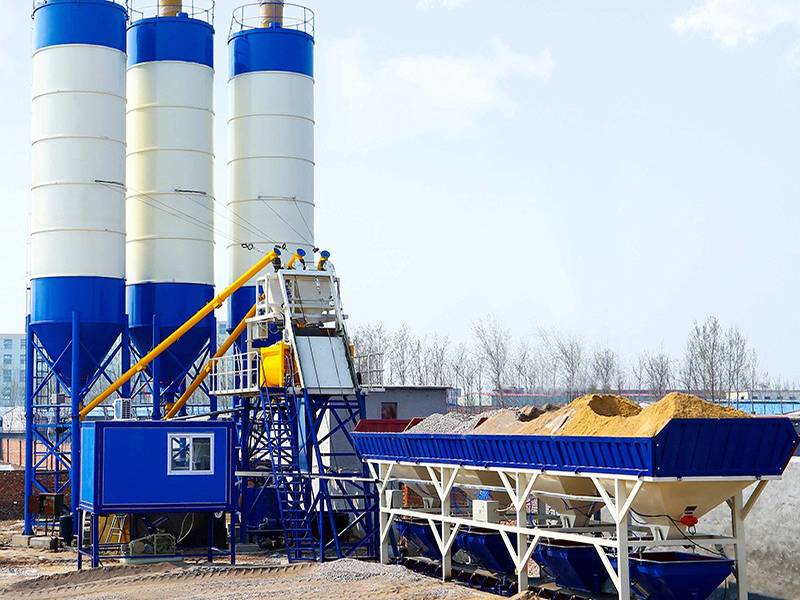
II. Concrete is Prone to Bleeding and Segregation
Cause
1. When the fineness of cement is large, it is easy to bleed; when the content of C3A in cement is low, it is easy to bleed; when the water consumption of standard consistency of cement is small, it is easy to bleed.
2. The cement dosage is small and easy to secrete water.
3. Concrete with low-grade cement is more prone to bleeding than concrete with high-grade cement (same dosage).
4. The same level of concrete, high-grade cement concrete is more prone to bleeding than low-grade cement concrete.
5. Concrete with large unit water consumption is prone to bleeding and segregation.
6. Concrete mixture temperature is too high, especially in summer, high temperature, rapid hydration reaction, slump loss.
7. Concrete with low strength grade is prone to bleeding.
8. Concrete with small sand ratio is prone to bleeding and segregation.
9. Continuous particle size gravel concrete bleeding less than single particle size gravel.
10. Concrete with poor water retention, thickening and air entraining properties of concrete admixture is prone to bleeding.
11. Excessive concrete admixture concrete prone to bleeding, segregation.
12. Some models of mixing trucks have poor mixing performance. After a certain distance of transportation, the concrete mixture obviously floats when it is initially discharged.
13. There is accumulated water in the mixing drum of the concrete mixing truck, and water is arbitrarily added to the mixing drum before loading or during transportation.
Solutions
1. The fundamental way is to reduce the unit water consumption.
2. Increase the sand ratio and choose a reasonable sand ratio.
3. Hot summer, take measures to reduce the temperature of concrete mixture.
4. Increase the dosage of cement or add proper amount of Grade I and II fly ash.
5. Using continuous graded gravel, and the needle flake content is small.
6. Improve the performance of concrete admixture, make it have better water retention, thickening, or reduce the amount of concrete admixture (only on site), if the mixing station reduces the amount of concrete admixture, it may lead to a new problem of rapid slump loss of concrete.
7. Before discharging, the concrete mixer truck should rotate the mixing drum at medium and high speed to make the concrete mixture even before discharging.
8. Strengthen management, the truck mixing drum after cleaning, must be drained of water before loading. After loading, it is forbidden to add water into the mixing drum at will.
Sum Up (the) Experience
We should optimize the mixture ratio, strengthen the incoming inspection of raw materials and strengthen on-site management. Put an end to the phenomenon of arbitrarily increasing water consumption due to poor on-site management of the mixing station.
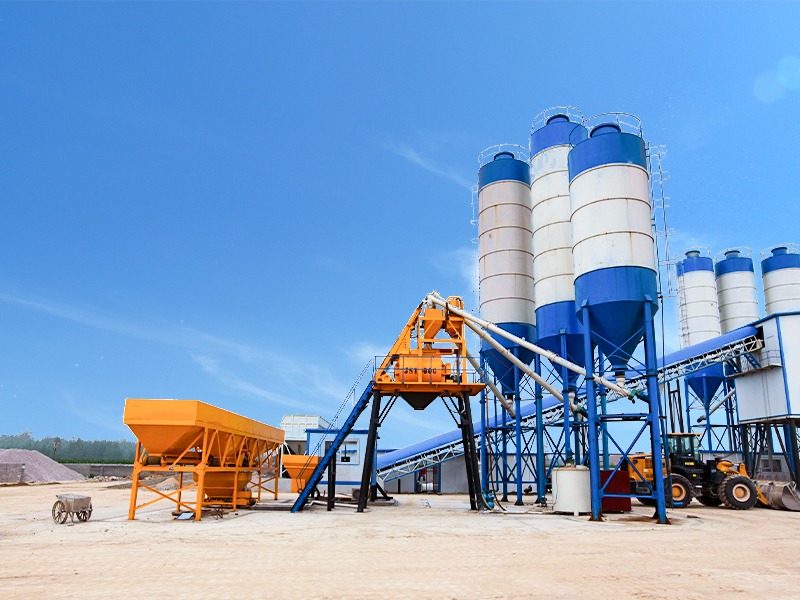
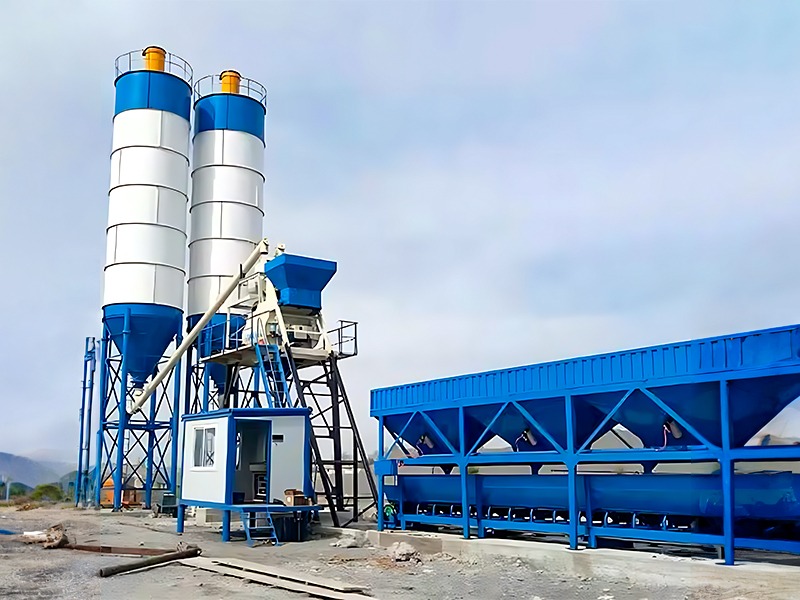
III. The Concrete Strength is Not Enough and The Homogeneity is Poor
Cause of occurrence
1. Mixer metering equipment failure, slump out of control, large dispersion of concrete strength.
2. Cement expired or be affected with damp, activity is reduced; Sand and stone aggregate gradation is not good, the gap is large, the silt content is large, there are many sundries, the admixture is used improperly, and the dosage is inaccurate.
3. Improper concrete mixture ratio and inaccurate measurement.
4. Add water at will during construction to increase the water cement ratio.
5. The concrete feeding order is reversed, the mixing time is not enough, and the mixing is uneven.
6. Winter construction, dismantle early or early freezing.
7. During construction in summer, the specimen was not covered and cured in time.
8. Concrete block production is not vibrating compaction, poor maintenance management, or maintenance conditions do not meet the requirements, in the same condition maintenance, early dehydration or broken by external forces.
Prevention and Control Measures
1. Cement should have the factory certificate, fresh without caking, expired cement only after passing the test. The particle size, gradation and silt content of sand and gravel should meet the requirements, and the concrete mixture ratio should be strictly controlled to ensure accurate measurement. The concrete should be mixed in sequence to ensure mixing time and uniform mixing. To prevent concrete from early freezing, the concrete prepared with ordinary cement in winter shed construction has a strength of more than 30%, and the concrete prepared with slag cement has a strength of more than 40% before it can be frozen. According to the requirements of construction specifications, the concrete upper test block should be carefully made and the management and maintenance of the test block should be strengthened.
2. Strengthen the maintenance of measuring equipment, ensure accurate feeding, control the machine concrete mixture slump.
3. The sampling on the construction site should be taken between 1/4 and 3/4 during the unloading process of the mixing truck, and the quantity should be 1.5 times of the required amount of concrete quality inspection items, and should not be less than 0.02m3. The artificial ramming test block should be put into the test mold in two layers, and the charging thickness of each layer is roughly equal. The number of ramming times of each layer should be determined according to the cross section of the specimen, generally not less than 12 times per 2500px2 cross-sectional area.
4. Strengthen the curing of test pieces, cover the surface of standard-raised test pieces after molding to prevent water evaporation and dehydration, and put them into a standard curing room with a temperature of 20+/-1℃ and a humidity of more than 95% after ripping the mold the next day. When there is no standard curing room, the concrete specimen can be cured in stagnant water with a temperature of 20 3℃, and the pH value of the water should not be less than 7.
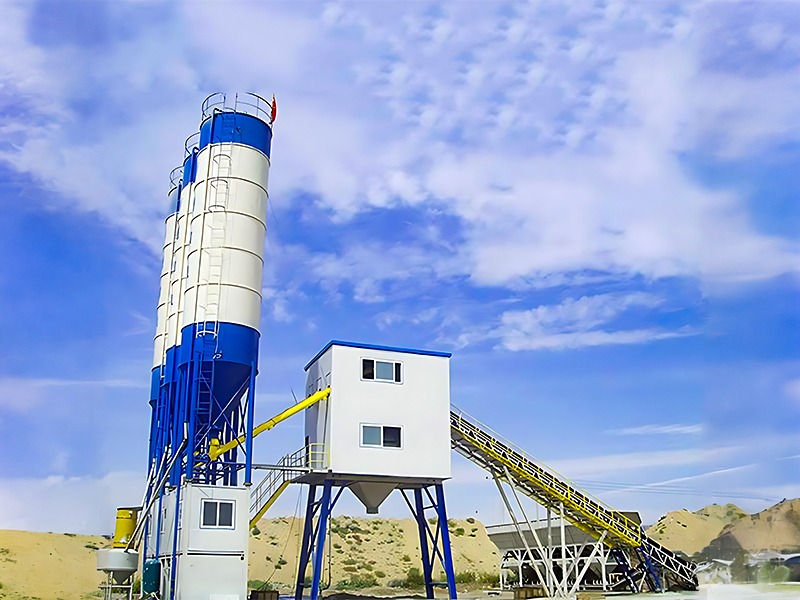
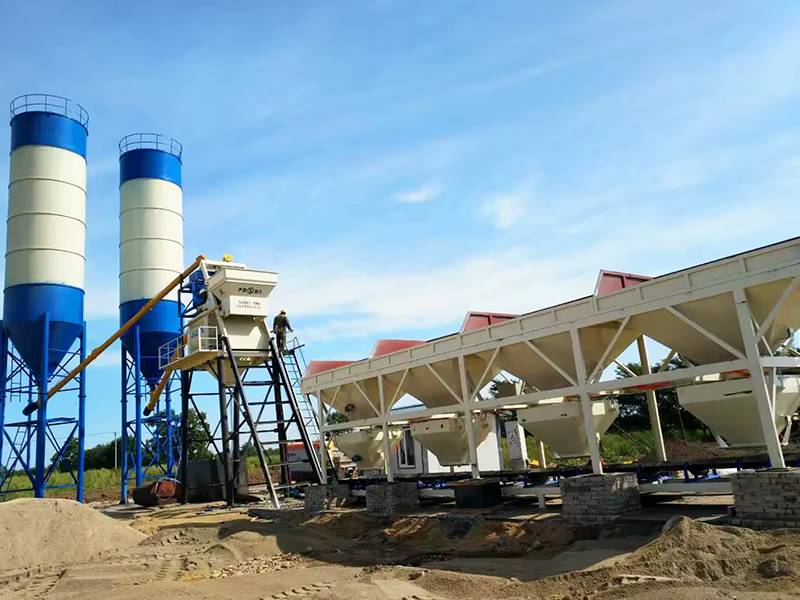
IV. The Mixing Station Quality Control Experience and Suggestions
The quality inspection of concrete is indispensable in that control of concrete quality management, and it is the main mean to ensure the quality of concrete. In the whole process of concrete production, transportation and construction, it plays an important role, and its main functions are as follows:
1. Do a good job of five checks and three prohibitions on supervision: raw material inspection, mix design, measurement, concrete mixing time, slump and strength; Unqualified materials are not allowed to be used, measuring equipment is not allowed to be produced, and unqualified concrete is not allowed to leave the factory to ensure that the concrete meets the quality requirements.
2. In strict accordance with the provisions of the specification random sampling, making test blocks, truthfully report, in order to really play the role of guiding production.
3. Do a good job in advance control, prevent quality accidents, through the quality inspection of raw materials and fresh concrete and quality supervision of the whole production process, grasp the quality dynamics of concrete in time, find problems in time, take timely measures to deal with them, prevent engineering quality accidents, and keep the quality of concrete in a stable state.
4. Feedback information, through the analysis of inspection data, grasp the quality of concrete and the changing law, to improve the concrete mix design, ensure the quality of concrete, make full use of additives and admixtures, reduce costs, strengthen management, etc., to provide the necessary information and basis.
5. Strengthen quality training, improve the technical level and quality awareness of operators, enhance the sense of responsibility, and ensure the qualified concrete quality. Regular and focused technical training for technicians and operators of concrete mixing stations will undoubtedly have obvious effects on saving costs, improving efficiency and further ensuring concrete quality.