Take You to Know More About the Mobile Concrete Mixer Truck
The concrete mixer truck industry has broad development prospects and potential. With the acceleration of global urbanization and the continuous advancement of infrastructure construction, the demand for concrete mixers continues to grow and the market scale continues to expand. Especially in developing countries such as China, the investment in infrastructure construction provides a broad market space for the mixer truck industry.
I. Introduction of mobile concrete truck mixer
Definition and working principle of ready mix concrete truck mixer
Concrete mixing truck mixer is a special vehicle for mixing, transporting and unloading concrete. It consists of chassis, concrete tank, feeding and discharging devices, hydraulic transmission system and cooling system. When the volumetric concrete mixer truck is working, cement, stones, sand and other raw materials are added into the tank, and the concrete is sent to the construction site through the discharge port after mixing.
II. Structure composition of mobile concrete truck mixer
The concrete mixer is mainly composed of chassis and upper part, and its structure can be subdivided into chassis system, hydraulic transmission system, mixing tank, discharging system, cleaning system, sub-frame, control system, idler system, feeding system and circuit system. The front end of the mixing tank is connected with the reducer and installed at the front of the frame, while the rear end is supported by two idler wheels installed at the back of the frame through a raceway.
Generally speaking, the concrete mixer also includes core components such as automobile chassis, mixing drum, transmission system and water supply device. Due to technical limitations, domestic mixer trucks usually use domestic core components with tank volume between 3 and 8 cubic meters, while most of them use imported components with tank volume above 8 cubic meters.
(1) Chassis system
Chassis is an important part of concrete truck mixer, and heavy truck chassis is usually used. The chassis is equipped with oil pump, hydraulic motor, cooler and other components to provide power and cooling for the concrete tank, and the chassis system is responsible for realizing the transportation function of the whole concrete mixer.
(2) Concrete mixing tank
Mixing drum is the core component of mixing truck, which is used to store concrete and plays a vital role in preventing concrete from curing and segregation. There are blades in the tank, which are mainly used for stirring and guiding materials. Tank is the most important part of concrete truck mixer, and it is also the basic facility for mixing, transporting and storing concrete. At present, tanks are mainly divided into round and polygonal forms, most of which are round tanks, usually made of steel plates, and their service life can reach several years.
(3) Feeding and discharging device
The feeding and discharging device is an important part of the concrete truck mixer, which consists of a feeding wheel, a discharging port, a concrete tank, mixing blades, an oil cylinder, a main discharging chute, an auxiliary discharging chute and a locking rod, among which the auxiliary discharging chute is used to extend the length of the main discharging chute, completing the work of adding and mixing concrete raw materials and discharging finished concrete.
(4) Hydraulic transmission system
The hydraulic transmission system is the core part of the concrete truck mixer. With the oil pump as the core, the concrete tank can be rotated, lifted and discharged through pipelines, oil cylinders, hydraulic motors and other devices. The system converts the power output by the engine through the power take-off into hydraulic energy (including displacement and pressure), and then into mechanical energy (including rotational speed and torque) through the motor, thus providing the required power for the rotation of the mixing drum.
(5) Cleaning system
The system includes pressure water tank, water gun, water pipe and valve, etc., and adopts air pressure water supply mode. It is mainly used to wash the hopper after loading, and to clean the mixing drum and discharging chute after discharging, so as to prevent concrete from sticking.
(6) Subframe
As the main load-bearing part of the mixer truck, the subframe bears almost all the loads during operation and transfers them to the chassis. At the same time, the subframe can also alleviate the impact load caused by road bumps and deceleration. The whole subframe consists of main beam, foreground support frame and background support frame.
(7) Control system
The system consists of controller, linkage shaft, flexible shaft and linkage mechanism, which is mainly responsible for controlling the speed and direction of rotation of the mixing drum.
(8) Roller system
Located at the back of the mixing tank, it is connected with the sub-frame and mainly plays the role of supporting the mixing tank.
(9) Feeding system
It consists of a feed hopper and a bracket, wherein the feed hopper is often subjected to impact wear, so the material is required to have good wear resistance; The bracket is mainly used to reduce the impact force.
(10) Circuit system
Covers the whole circuit layout of the mixer, including key components such as taillights, side marker lights, position lights and cooling fan motors.
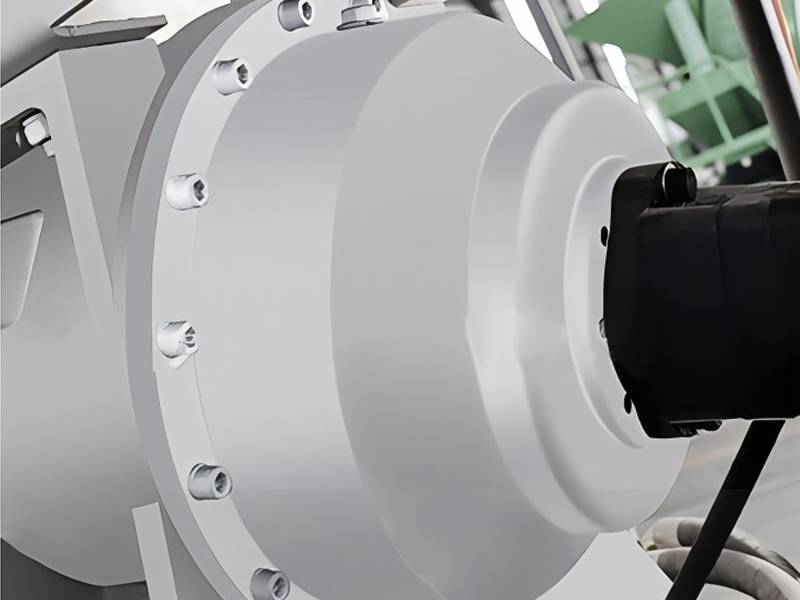
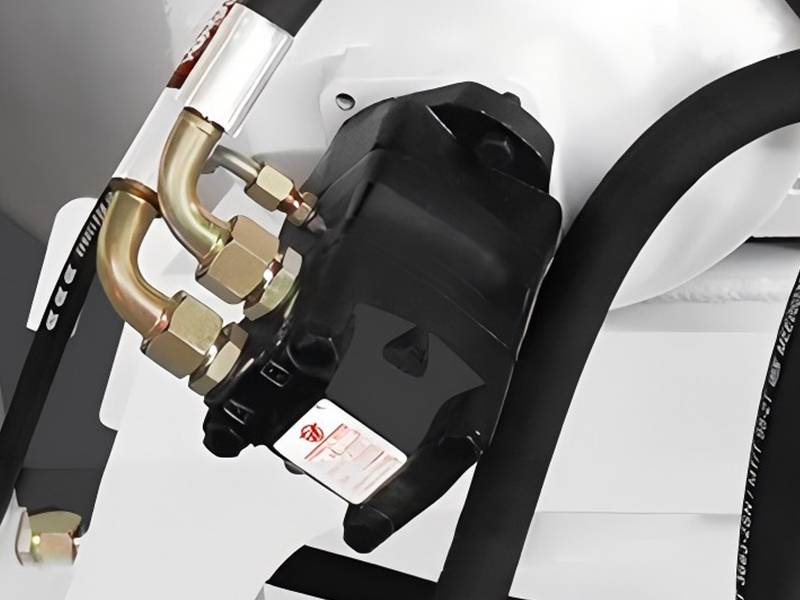
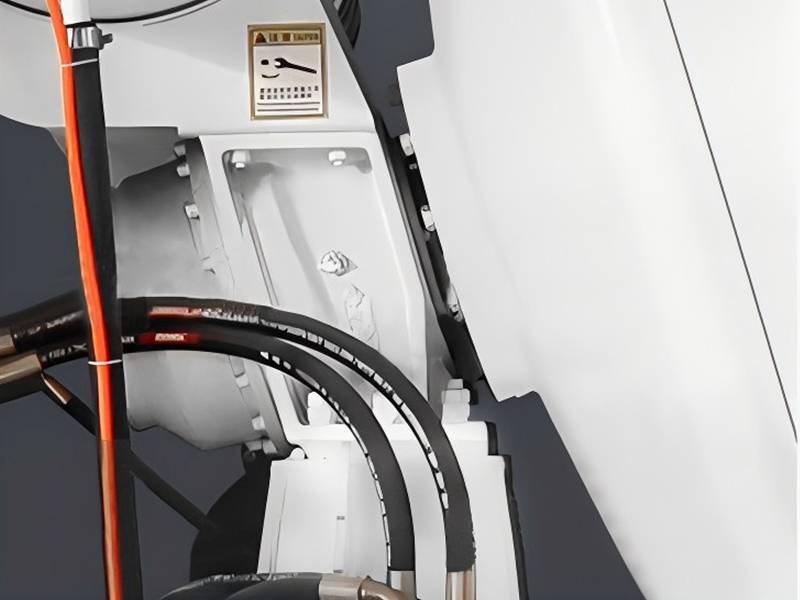
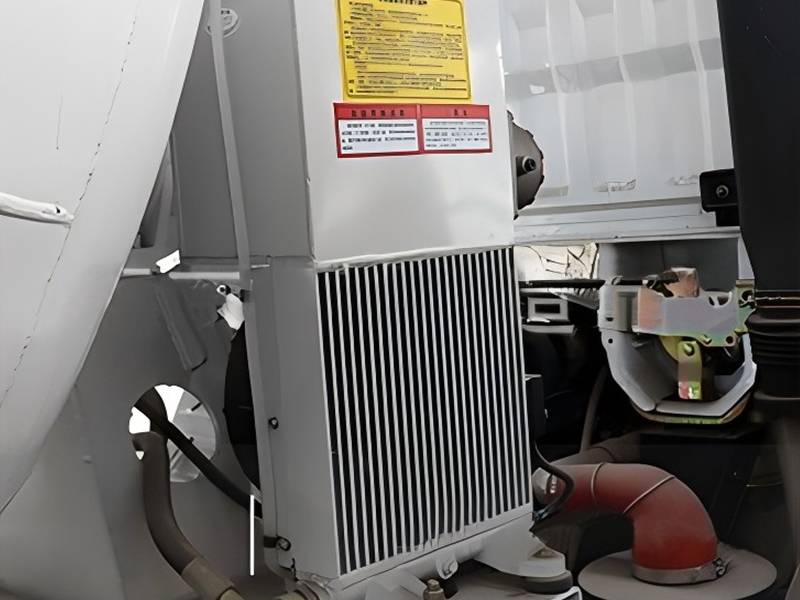
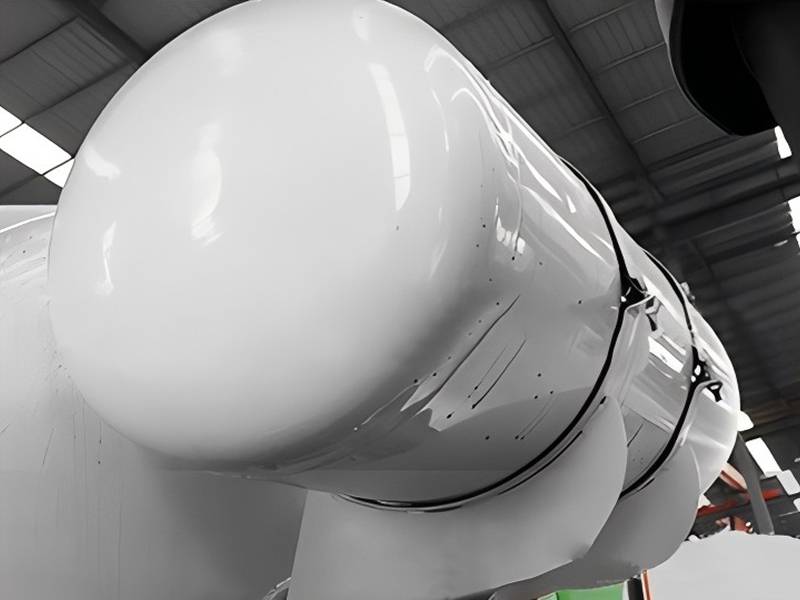
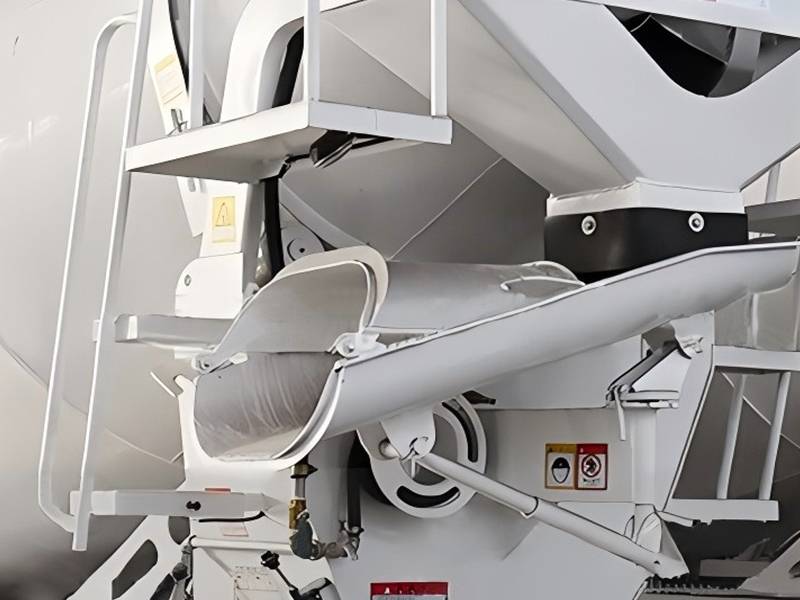
III. Usage scene of mobile concrete truck mixer
Concrete truck mixer is mainly used for mixing, transporting and unloading concrete, which is widely used in industrial and civil buildings, municipal engineering, water conservancy and electric power and other fields, especially in places far away from batching stations and on-site concrete preparation.
IV. Dimensions of mobile concrete truck mixer
Concrete mixers vary in size. The capacity of small mixers is usually between 3 and 8 cubic meters, while that of large mixers can range from 12 cubic meters to 15 cubic meters. What is more common in the market is a 12 cubic meter mixer. These mixers are divided into different specifications according to the volume, such as 3 cubic meters, 3.5 cubic meters, 4 cubic meters, etc., until 16 cubic meters. The main difference between mixer trucks of different specifications lies in their loading capacity. The larger the volume, the more concrete they can load and the higher the price.
When choosing a mixer, the appropriate volume should be determined according to the purpose of buying a car and the use scenario. If it is transported at the price per cubic meter of concrete, it is more cost-effective to choose a large-capacity mixer; If monthly transportation is carried out, a 12 cubic meter mixer truck can usually meet the basic needs.
VI. Maintenance of mobile concrete truck mixer
(1) Regularly check and maintain the hydraulic transmission system and tank body.
(2) Regularly check the wear degree of the tank mixing blades and replace the damaged parts in time.
(3) Regularly clean and brush the tank body to avoid mildew and rust of concrete.
(4) Maintain the inside of the tank, regularly clean up the residue, clean the tank and remove the dirt of lubricating oil and car wash liquid.
(5) Regularly check and replace the wearing parts such as oil, liquid and filter element of the vehicle.
Through the introduction of the concrete truck mixer, I believe you have a deeper understanding of its definition, structure, working principle and usage scenarios. At the same time, the concrete truck mixer also needs frequent maintenance in the process of use to ensure its normal operation and improve work efficiency.