Comparison Between Horizontal and Vertical Cement Storage Silos
In industrial production, horizontal and vertical storage tanks are two common powder material storage equipment. They exhibit significant differences in structure, functionality, and application scenarios. This article provides a comprehensive comparison of the advantages and disadvantages of horizontal and vertical storage tanks to help you better understand the characteristics of these two types of equipment.
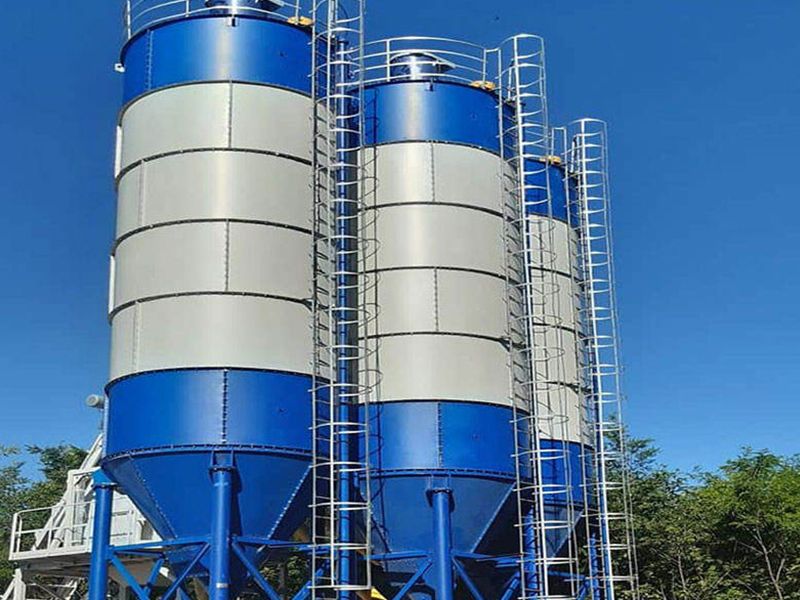
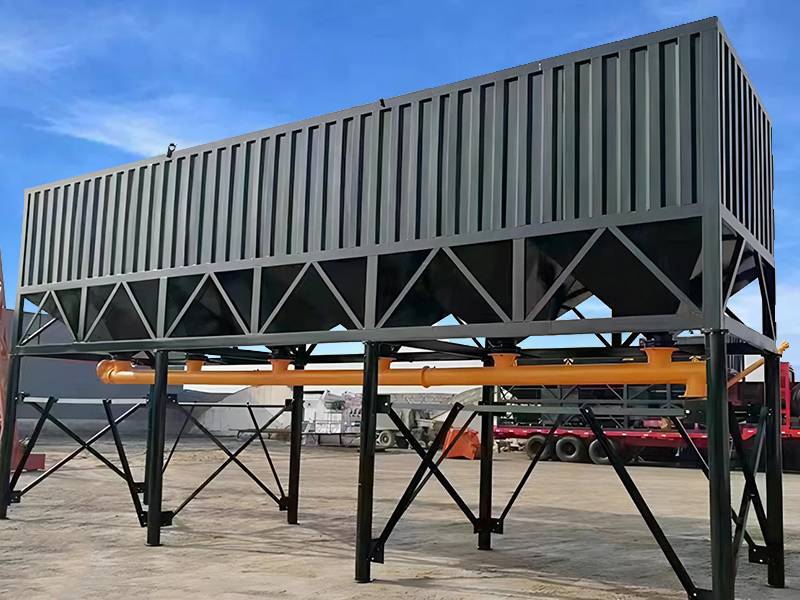
I. Structure and Appearance
1. Vertical Cement Storage Silo:
Features a vertical structure, typically made of steel.
The bottom is cone-shaped, minimizing footprint.
Has a relatively high height, usually ranging from 8 to 15 meters.
2. Horizontal Cement Storage Silo:
Also known as a square cement silo or foundation-free cement silo.
Supported by several legs at the bottom, with the silo body welded from high-quality steel.
Relatively low in height, generally around 4.5 meters, making it suitable for workshops and height-restricted areas.
II. Application Scenarios and Advantages
1. Vertical Cement Storage Silo:
Suitable for outdoor use, especially in spacious areas with no height restrictions.
Structurally stable, capable of bearing significant pressure and weight.
Large capacity, customizable from tens to hundreds of tons based on demand.
Quick discharging with minimal residue, simple and convenient operation.
Excellent waterproof performance, with a sealed design preventing water infiltration.
Durable, capable of stable operation over a long period.
2. Horizontal Cement Storage Silo:
Suitable for indoor use or height-restricted areas.
Requires no foundation, reducing height and facilitating easy installation, disassembly, and mobility.
Large capacity, with horizontal dimensions allowing for greater storage, meeting large-scale production needs.
Available in standard models of 50 tons, 60 tons, 80 tons, 100 tons, 150 tons, and 200 tons, also customizable based on site requirements.
Easy installation, with a relatively simple structure, saving time and costs, as it can be placed on hardened ground.
High stability, with a low center of gravity preventing tilting or overturning.
Convenient transportation, fitting within standard vehicle height and width limits, transportable by a 6-meter truck.
Environmentally friendly and energy-saving, meeting environmental requirements and reducing dust emissions.
III. Disadvantages
1. Vertical Cement Storage Silo:
Requires complicated infrastructure for tank legs and secure welding.
Installation is challenging due to the complex structure, increasing time and cost.
Lower stability, with the high center of gravity making it prone to wind and lightning risks.
2. Horizontal Cement Storage Silo:
Height limitation: Due to its horizontal design, the height is restricted, potentially unable to meet specific production scenarios.
Outlet position: The outlet is usually at the bottom, requiring additional conveying equipment or operational adjustments for certain applications.
IV. Cost and Maintenance
1. Vertical Cement Storage Silo:
Lower cost but may require additional safety measures and expenses due to its height.
Relatively simple maintenance but requires regular inspections and cleaning.
2. Horizontal Cement Storage Silo:
May have slightly higher costs, but overall cost-effectiveness is high considering its mobility and flexibility.
Easy maintenance, facilitating cleaning and repairs, extending equipment lifespan.
V. Application Fields
1. Vertical Cement Storage Silo:
Widely used in construction, water conservancy, and highway engineering.
Suitable for large-scale projects, meeting various engineering needs.
2. Horizontal Cement Storage Silo:
Used in small mortar stations, building material production enterprises (e.g., putty powder, tile adhesive, thermal insulation mortar) for powder and sand storage.
Also suitable for cement storage in mobile concrete mixing stations.
In summary, vertical and horizontal cement storage silos each have unique advantages and application scenarios. When selecting, comprehensive consideration should be given to specific usage requirements, site conditions, cost budgets, and other factors. In certain specific application scenarios, such as large-scale production, space-limited environments, or situations requiring frequent monitoring and maintenance, horizontal storage tanks may be more advantageous. In other scenarios, such as those requiring flexible height adjustments, convenient discharging, or space-saving, vertical storage tanks may be more suitable.